Bowl & Mantle Liner is manufactured with high manganese steel Mn13Cr2, Mn18Cr2, Mn22Cr2 or Manganese steel with special alloy and heat-treatment process. Bowl & Mantle Liner has a working life of 10%-15% longer than those made of traditional manganese steel. As per the feedback from customers, the good performance of our Bowl & Mantle Liner
in different working condition greatly decreased the time of examination & repair and the use-cost.
MAIN BRANDS SUPPORT:
Metso, Sandvik, Barmac, SVEDALA, Omnicone, EXTEC, Maxtrak, Keestrack, Symons, Hazemag, Cedarapids, Telsmith, McCloskey, Trio, Powerscreen, Kleemann, Terex, Pegson, Kue Ken, Parker, Shanbao, SBM, Zenith, LIMING, MINYU and other famous brands.
MAIN MODELS SUPPORT:
Metso HP100HP200HP300 HP350 HP400HP500 HP700 HP800 HP3 HP4 HP5 G11M GP11FGP100 GP250 GP500 GP100S GP200 GP200S GP200SE GP300 GP300S GP500S GP300MF GP550 MP800 MP1000
Sandvik H2800 H3800 H4800 H6800 H7800 H8800 S2800 S3800 S4800 S6800 C-C2H36" C-C2H36" S11-36" MC-C2H36"
MINYU MCC51/MCC1300, MCC600, MCSH48, MCF40/MCC1000, MCF54, MCSH42H, MCF45/MCF1150 MCF51/MCF1300 MCSS36, MCSH54/MCS1370, MCSH54, MCC40/MCC1000, MCF900, MCSS52/MCSS1370, MCC45/MCC1150, MCC54/MCC1370, MCC48/MCC1200, MCC45/MCC1150, MCC40/MCC1000, MCC54, MCSH42H, MCSS52/MCSS1370, MCSH51, MCSH30/MCS1000, MCSH36
Symons 3FT 4FT 4 1/4 FT 5 1/2FT 7FT 5100 4800
Terex Pegson/Terex Cedarapid Maxtrak 1000/TC1000, Maxtrak1300/TC1300, Trakpactor 428/4242SR, Trakpactor 1412,RC36, RC45, RC54, RC60, RCII45, RCII54,MVP280, MVP380, MVP450, MVP550
Telsmith 36S&FC, 48S&FC,52S&FC, 66S&FC ,SBS Models: 38SBS, 44SBS, 57SBS, 68SBS
Product Package of Bowl & Mantle Liner
Steel Pallet.
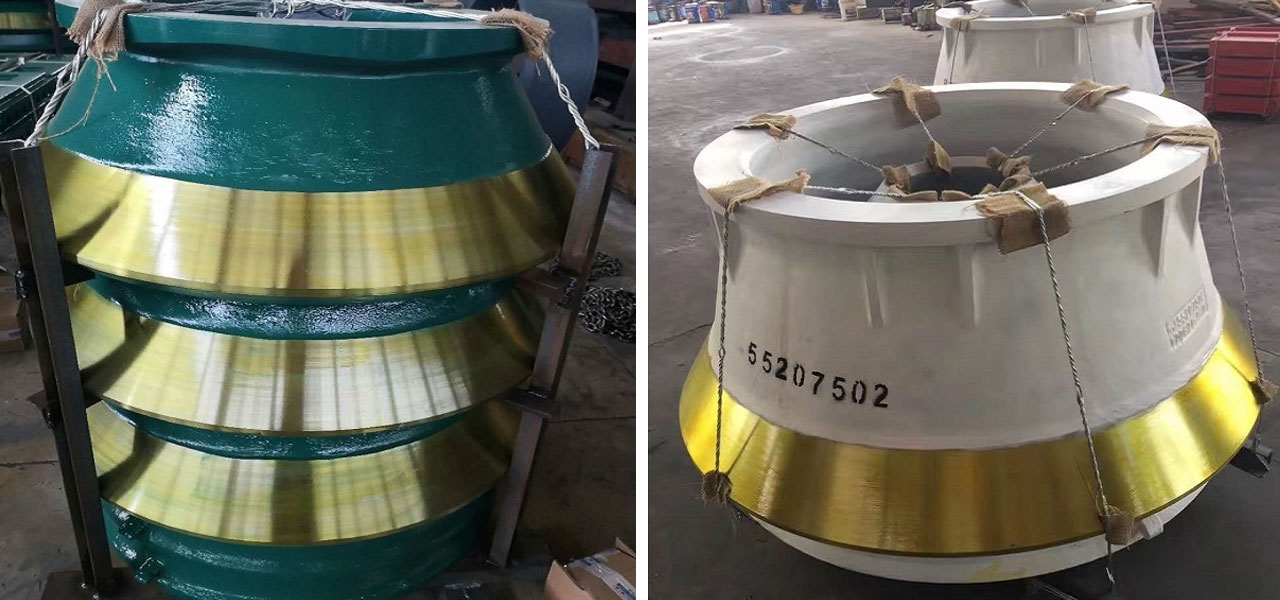
Customized according to special packing requirement
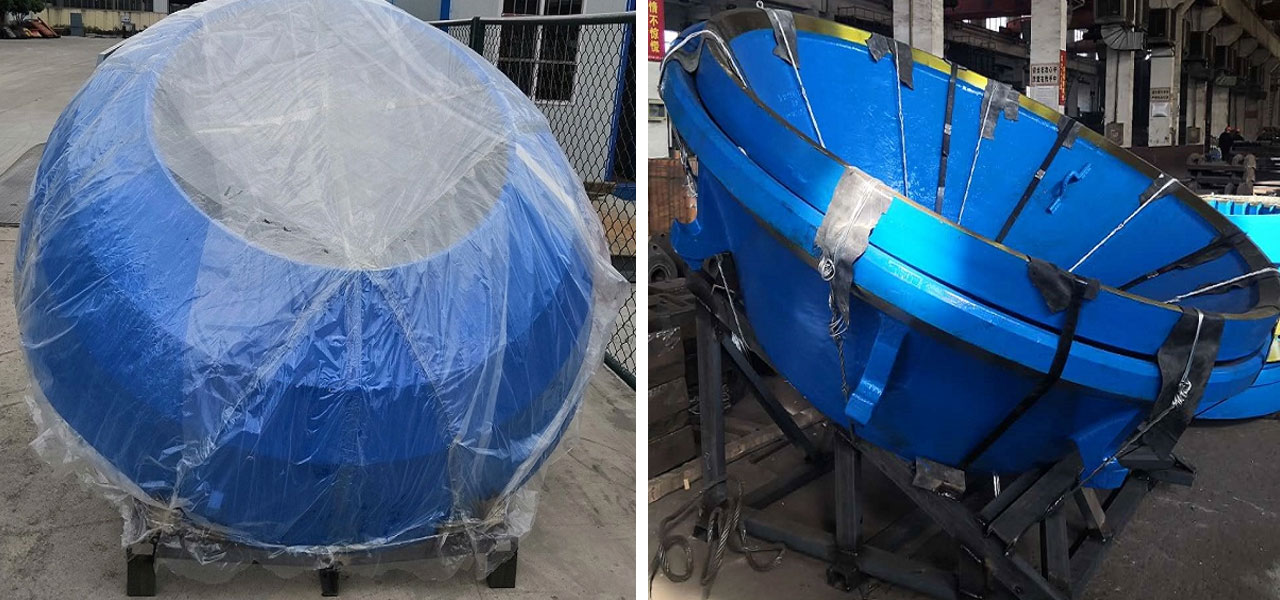
Application of Bowl & Mantle Liner
Bowl & Mantle Liner is main wearing parts for cone crusher in the crushing plant. Our Bowl & Mantle Liner are widely used in the mining industry, stone crushing plant, aggregate / quarry plant, construction industry and others.
Cone crushers resemble gyratory crushers from technological standpoint, but unlike gyratory crushers, cone crushers are popular in secondary, tertiary, and quaternary crushing stages. Sometimes, however, the grain size of the processed material is small enough by nature and the traditional primary crushing stage is not needed. In these cases, also cone crushers can carry out the first stage of the crushing process.
Cone crushers have an oscillating shaft, and the material is crushed in a crushing cavity, between an external fixed element (bowl liner) and an internal moving element (mantle) mounted on the oscillating shaft assembly.
An eccentric shaft rotated by a gear and pinion produces the oscillating movement of the main shaft. The eccentricity causes the cone head to oscillate between open side setting and closed side setting discharge opening.
The fragmentation of the material results from the continuous compression that takes place between the liners around the chamber. An additional crushing effect occurs between the compressed particles, resulting in less wear of the liners. This is called interparticular crushing also.
The cone crushers are equipped with a hydraulic setting adjustment system, which adjusts closed side setting and thus affects product gradation.
Depending on cone crusher, setting can be adjusted in two ways. The first way is for setting adjustment to be done by rotating the bowl against the threads so that the vertical position of the outer wear part (concave) is changed. One advantage of this adjustment type is that liners wear more evenly.
Another principle is that of setting adjustment by lifting or lowering the main shaft. An advantage of this is that adjustment can be done continuously under load.
To optimize operating costs and improve the product shape it is recommended that cone crushers are always be choke fed, meaning that the cavity should be as full of rock material as possible. This can be easily achieved by using a stockpile or a silo to regulate the inevitable fluctuation of feed material flow. Level monitoring devices detect the maximum and minimum levels of the material, starting and stopping the feed of material to the crusher, as needed.
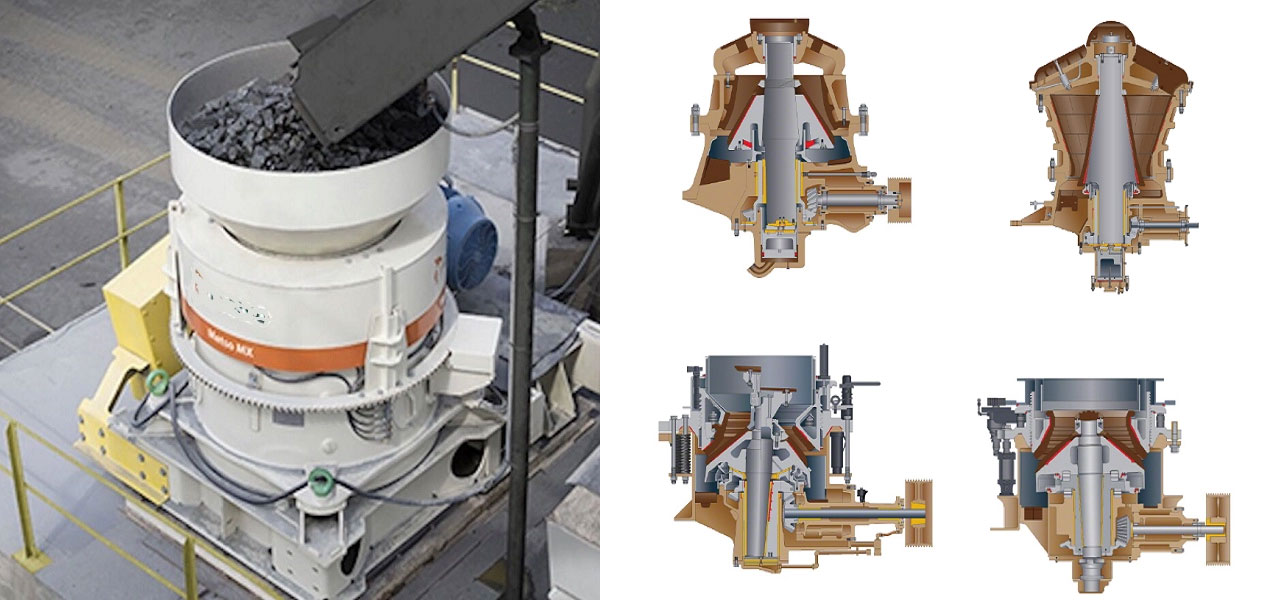
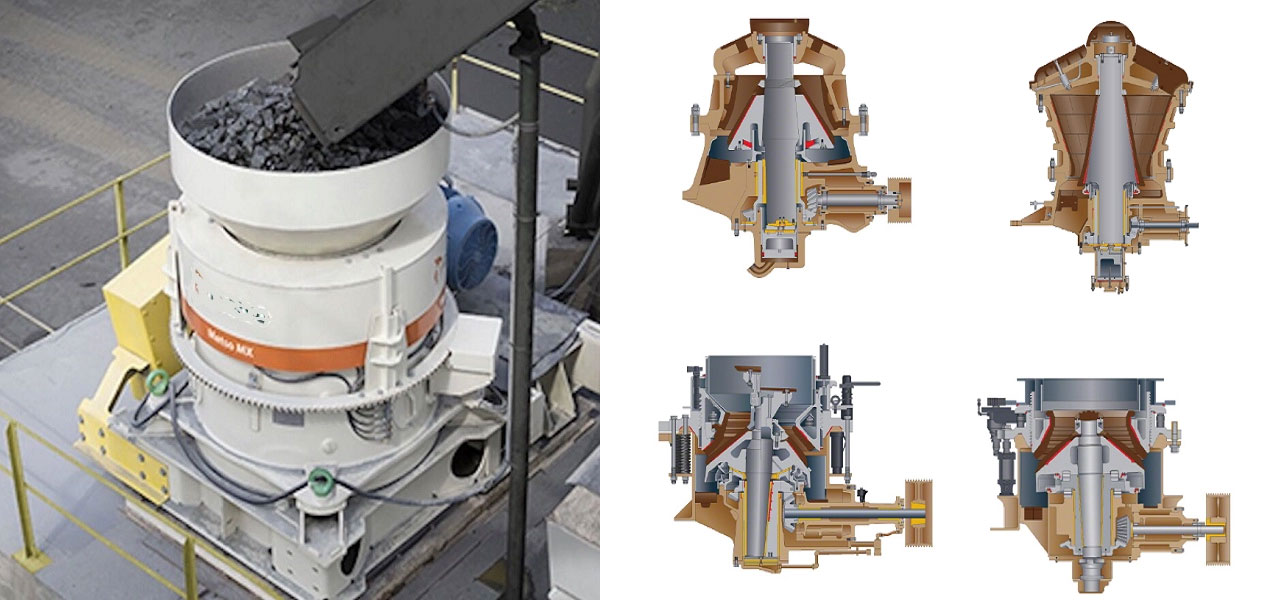