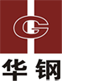
Name
|
Chemical Composition(%) |
|||||||
C |
Si |
Mn |
Cr |
Mo |
Cu |
P |
S |
|
Mn14 Mill Liner |
0.9-1.5 |
0.3-1.0 |
11-14 |
0-2.5 |
0-0.5 |
≤0.05 |
≤0.06 |
≤0.06 |
Mn18 Mill Liner |
1.0-1.5 |
0.3-1.0 |
16-19 |
0-2.5 |
0-0.5 |
≤0.05 |
≤0.06 |
≤0.06 |
Name |
Surface Hardness(HB) |
Impact value Ak(J/cm2) |
Microstructure |
Mn14 Mill Liner |
≤240 |
≥100 |
A+C |
Mn18 Mill Liner |
≤260 |
≥150 |
A+C |
C -Carbide | Carbide A-Retained austenite | Austenite |
Name
|
Chemical Composition(%) |
|||||||
C |
Si |
Mn |
Cr |
Mo |
Cu |
P |
S |
|
High Chrome Alloy Liner |
2.0-3.6 |
0-1.0 |
0-2.0 |
8-26 |
≤3.0 |
≤1.2 |
≤0.06 |
≤0.06 |
Middle Chrome Alloy Liner |
2.0-3.3 |
0-1.2 |
0-2.0 |
4-8 |
≤3.0 |
≤1.2 |
≤0.06 |
≤0.06 |
Low Chrome Alloy Liner |
2.1-3.6 |
0-1.5 |
0-2.0 |
1-3 |
0-1.0 |
≤1.2 |
≤0.06 |
≤0.06 |
Name |
Hardness HRC |
Microstructure |
High Chrome Alloy Liner |
≥58 |
M+C+A |
Middle Chrome Alloy Liner |
≥48 |
M+C |
Low Chrome Alloy Liner |
≥45 |
M+C+P |
Code
|
Chemical Elements(%) |
|||||||
C |
Si |
Mn |
Cr |
Mo |
Cu |
P |
S |
|
L2B |
0.6-0.9 |
0.4-0.7 |
0.6-1.0 |
1.8-2.1 |
0.2-0.4 |
0.3-0.5 |
≤0.04 |
≤0.06 |
L2C |
0.3-0.45 |
0.4-0.7 |
1.3-1.6 |
2.5-3.2 |
0.6-0.8 |
0.3-0.5 |
≤0.04 |
≤0.06 |
Code |
Hardness(HB) |
Ak(J/cm2) |
Microstructure |
L2B |
325-375 |
≥50 |
P |
L2C |
350-400 |
≥75 |
M |
M-Martensite, C-Carbide, A-Austenite, P-Pearlite |
Name |
C |
Si |
Mn |
Ni |
Cr |
S |
P |
Mo |
Hardness |
Ni-Hard AS2027 Gr Ni Cr 1-550 |
3.2-3.6 |
0.3-0.8 |
0.2-0.8 |
3.0-5.0 |
1.5-3.0 |
≤0.12 |
≤0.15 |
≤0.5 |
550-600HBN |
Ni-Hard AS2027 Gr Ni Cr 2-550 |
2.8-3.2 |
0.3-0.8 |
0.2-0.8 |
3.0-5.0 |
1.5-3.0 |
≤0.12 |
≤0.15 |
≤0.5 |
500-550HBN |
Ni-Hard AS2027 Gr Ni Cr 2-550 |
3.2-3.6 |
1.5-2.2 |
0.2-0.8 |
4.0-5.5 |
8.0-10.0 |
≤0.12 |
≤0.15 |
≤0.5 |
630-670HBN |
Name
|
Chemical Composition(%) |
|||||||
C |
Si |
Mn |
Cr |
Mo |
Cu |
P |
S |
|
White Iron Steel Liner |
2.0-3.3 |
0-0.8 |
≤2.0 |
12-26 |
≤3.0 |
≤1.2 |
≤0.06 |
≤0.06 |
Name |
HRC |
Ak(J/cm2) |
Microstructure |
White Iron Steel Liner |
≥58 |
≥3.5 |
M+C+A |
M-Martensite C- Carbide A-Austenite |